Introduction
PZLASER has positioned itself in the dynamic world of beauty technology as a leader in innovation and reliability. At the core of our success is an unwavering dedication to precision engineering and stringent quality control. Each machine leaving PZLASER manufacturing factory is a testament to excellence, blending advanced craftsmanship with rigorous standards.
This commitment ensures superior performance and long-term dependability, earning the trust of clients worldwide. Explore the intricacies of the PZLASER manufacturing process, where cutting-edge equipment, skilled craftsmanship, and strict adherence to international standards come together to create exceptional beauty devices designed to elevate both aesthetics and functionality.
High-Standard Production Workshops: The Backbone of Excellence
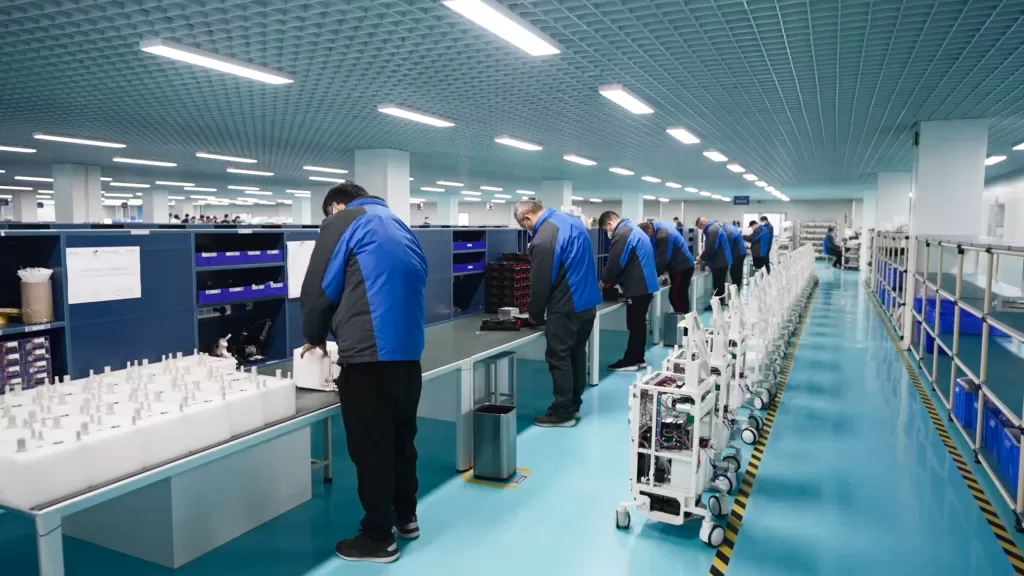
Every PZLASER machine begins its journey in our state-of-the-art professional production workshops, purpose-built to meet international quality management standards. From temperature-controlled environments to ergonomically designed workstations, every aspect reflects a dedication to perfection.
Our workshops are equipped with advanced tools and machinery to ensure precision at every production stage during PZLASER manufacturing process. By merging modern technology with expert craftsmanship, we produce beauty devices that set new industry benchmarks. This seamless combination of innovation and expertise creates a strong foundation for each device, ensuring structural integrity and optimal performance.
Beyond being a workspace, our production area is a hub of creativity and innovation, where new ideas are transformed into functional solutions. From prototypes to full-scale production, every step is executed with meticulous attention to quality, ensuring consistency for our partners and end-users.
Internal Mechanical Component Assembly
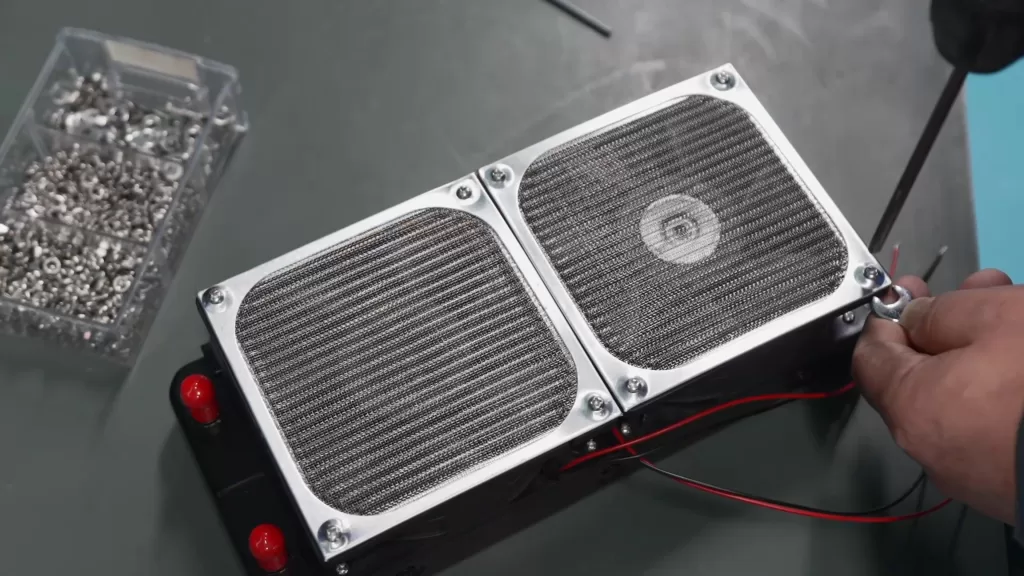
The mechanical components form the heart of any beauty device. During PZLASER manufacturing process, the assembly of internal parts is a process driven by precision and guided by adherence to strict international standards.
Our skilled technicians carefully assemble each component, ensuring every part integrates perfectly into the design. This stage is critical, as even the slightest deviation could impact the device’s functionality. By employing advanced assembly methods and automated systems, we ensure every machine operates efficiently and delivers flawless results.
Each component undergoes rigorous inspection to identify and eliminate imperfections before assembly. This proactive approach guarantees efficiency and durability, enabling our devices to withstand years of intensive use without compromising quality.
Framework Construction: Building a Reliable Skeleton
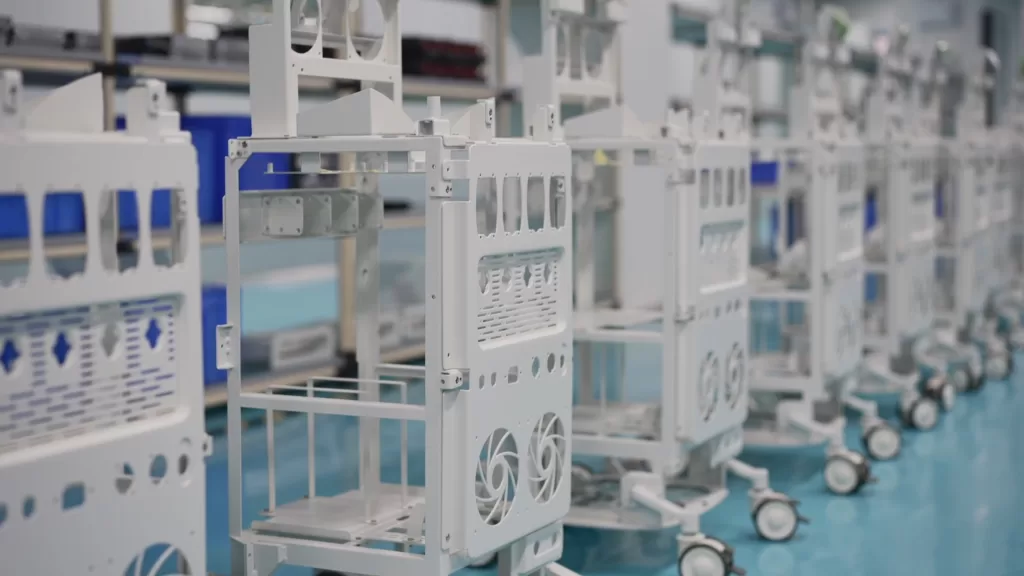
Every great device begins with a solid framework. At PZLASER, we prioritize using high-quality materials to construct the skeleton of our machines. These materials undergo rigorous testing to ensure they can support the intricate mechanisms housed within them.
Our framework construction process combines precision processing with detailed design schematics. From laser-cut components to welded joints, our engineers scrutinize scrutinize every detail for structural integrity. Therefore, this kind of robust skeleton provides a stable and reliable platform for seamless operation.
By focusing on even the smallest details during this phase, we create devices that are not only highly functional but also resilient, and capable of maintaining peak performance in diverse conditions and applications.
Electrical Components Installation During PZLASER Manufacturing Process
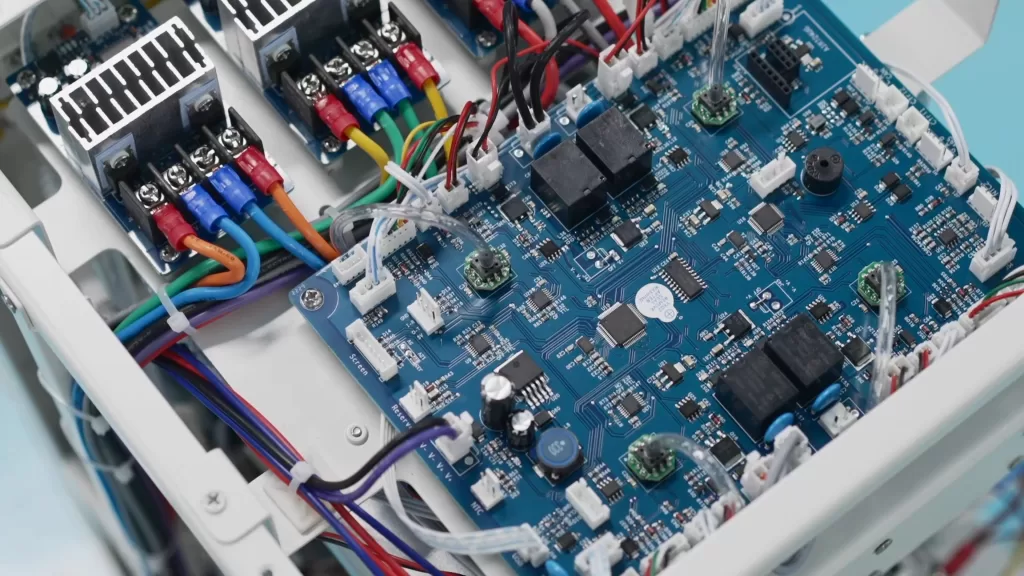
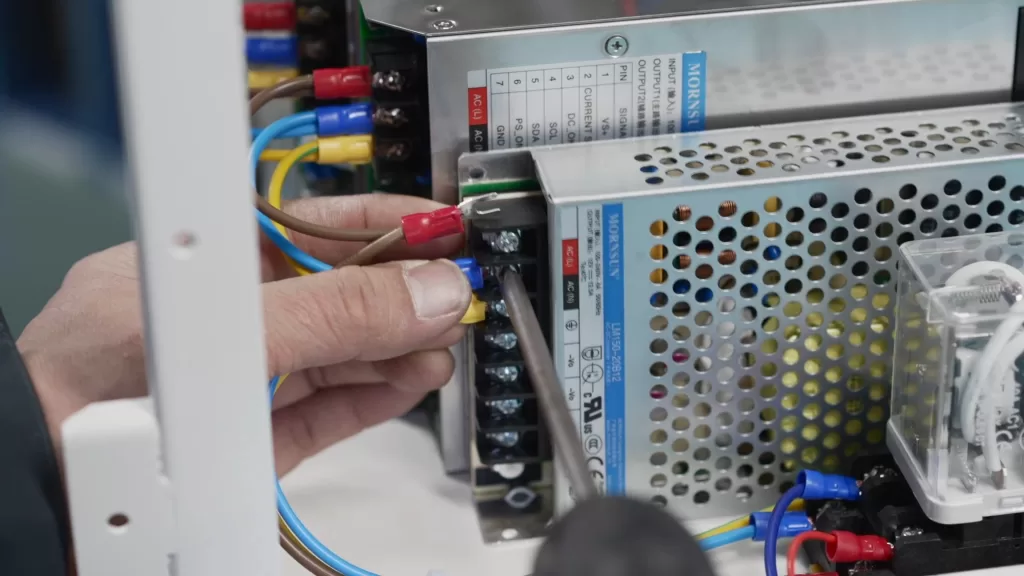
The electrical system acts as the nervous system of our devices, powering their functionality and precision. At PZLASER factory, we follow stringent protocols for installing and connecting electrical components, ensuring every wire, connector, and circuit meets our exacting standards.
Precision is critical at this stage, as even minor errors can disrupt the entire system. We meticulously test each connection to ensure stability and reliability, delivering a consistent power supply to the machine.
Utilizing advanced diagnostic tools, we optimize the electrical systems to support the innovative features that set PZLASER devices apart in the beauty industry.
Precision Component Assembly in Cleanroom
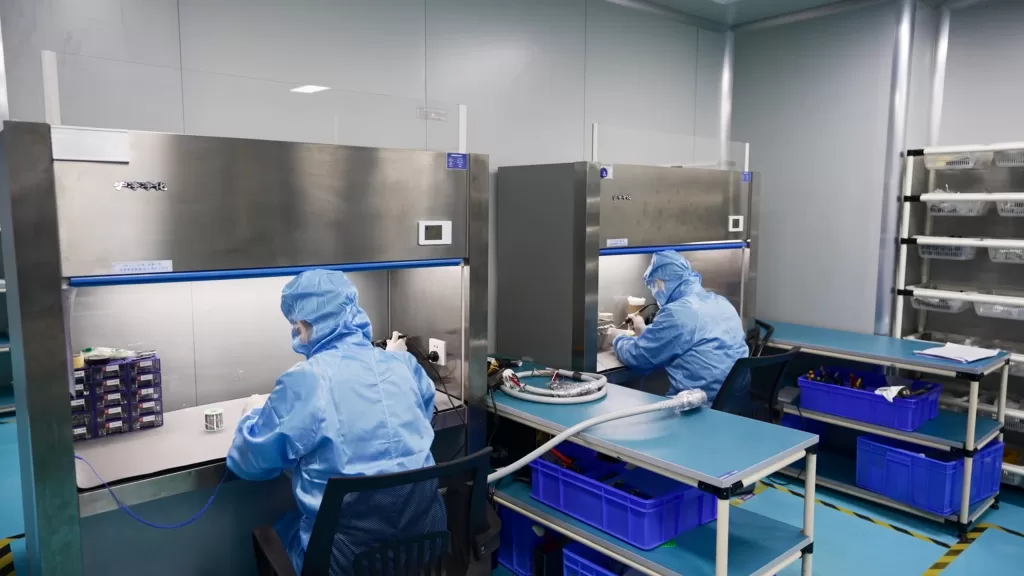
Core components require an environment free of contaminants to ensure precision and longevity. PZLASER’s state-of-the-art cleanrooms maintain ultra-low levels of particulate matter, providing a controlled environment for assembling the most sensitive and critical parts.
From optical lenses to ultrasonic transducers, we handle every component with exceptional care and precision. Advanced cleanroom technology eliminates the risk of contamination that could compromise functionality or reduce lifespan.
This meticulous process guarantees unmatched accuracy and performance, setting new standards for reliability in the beauty equipment industry.
Finishing Touches: Installation of Exterior Casings
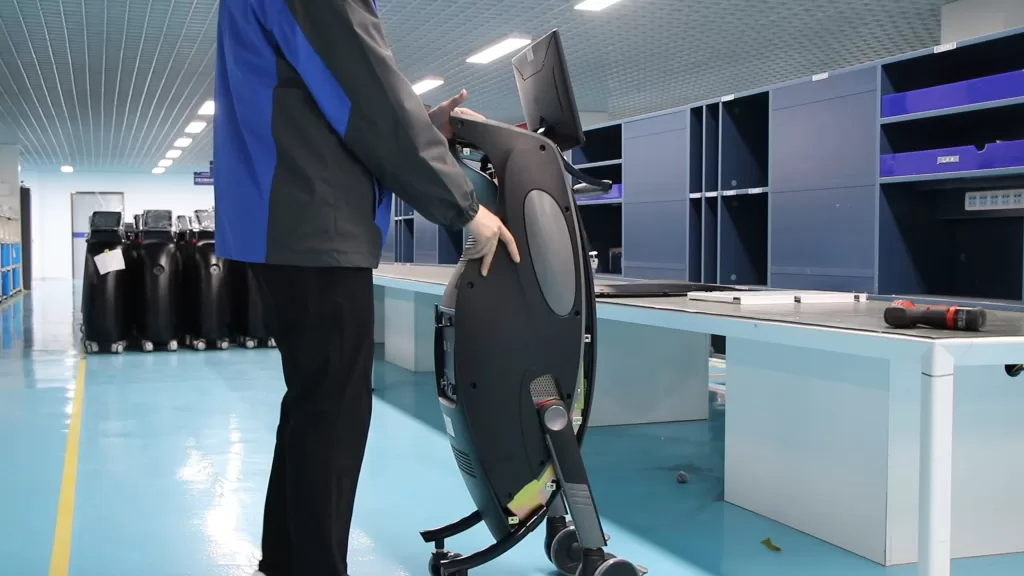
A machine’s exterior is more than just a protective shell—it’s a statement of quality and design. After PZLASER manufacturing process, each molded casing is carefully aligned and installed to seamlessly fit the internal framework.
Using detailed schematics, our technicians ensure that every casing is both aesthetically pleasing and structurally secure. The result is a flawless outer shell that not only protects the internal components but also enhances the machine’s visual appeal.
This process ensures durability and creates a polished, professional appearance that resonates with users worldwide.
Rigorous Appearance Inspection After Initial Installation
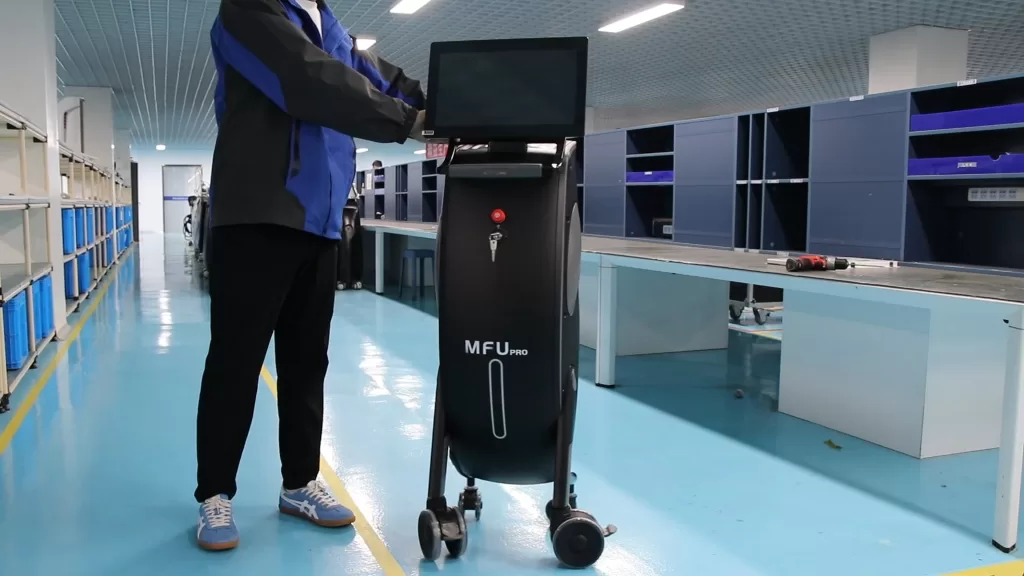
Attention to detail is critical in quality assurance. After assembly, each machine undergoes a comprehensive visual inspection to verify its appearance and structural integrity.
Our inspectors carefully examine every surface, joint, and seam to ensure there are no blemishes, misalignments, or weak points. Additionally, we check casings for a secure fit and evaluate the overall design for compliance with aesthetic and functional standards.
This rigorous manufacturing process ensures that every PZLASER equipment is not only operationally flawless but also visually impeccable, reflecting the premium quality of our brand.
Testing and Debugging: Perfecting Performance
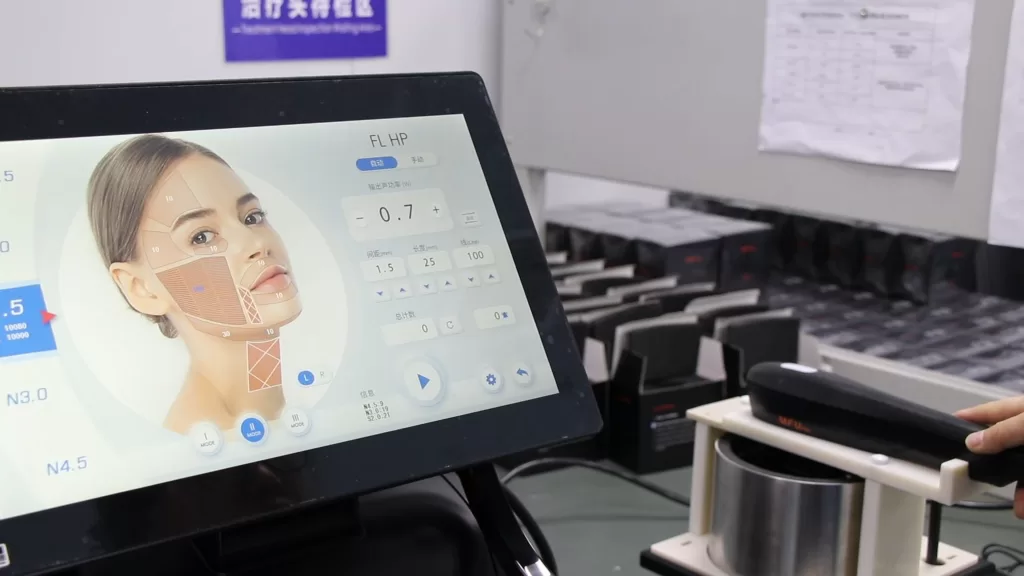
Performance always lies at the heart of PZLASER’s reputation for excellence. Every machine undergoes extensive testing and debugging to ensure all features function as intended.
From basic functionality checks to advanced stress tests, no detail is overlooked. We test each device in real-world scenarios to verify performance under varying conditions. This exhaustive process ensures consistent results, exceeding the expectations of professionals and end-users alike.
Our team identifies and resolves any issues at this stage, ensuring that every device operates with absolute precision and reliability.
Ready for Delivery: Machines in Prime Condition
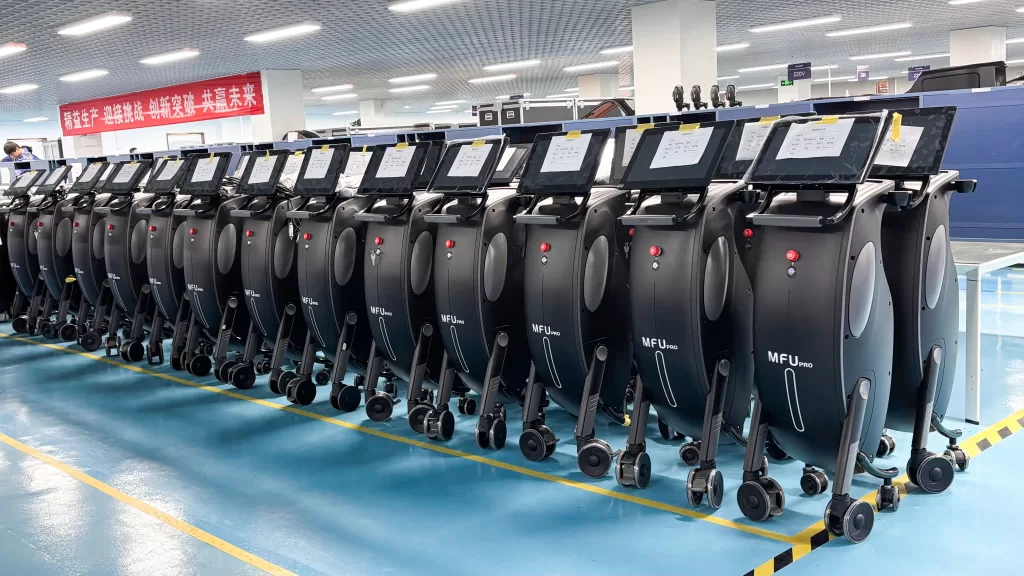
After passing all tests and inspections, each PZLASER machine is prepared for delivery in prime condition, ready to perform at its best right out of the box.
Particularly, the laser beauty machines manufactured by the PZLASER factory have passed various professional certifications such as FDA, Medical CE, and NMPA, ensuring their superiority in professionalism and quality.
Our dedication to quality extends to packaging and logistics, ensuring each machine arrives in perfect condition. This commitment to excellence ensures that beauty professionals worldwide can achieve remarkable results with our devices.
Conclusion
At PZLASER, manufacturing excellence is more than a goal—it’s a philosophy that drives everything we do. From meticulous assembly to rigorous testing, every step of the PZLASER manufacturing process reflects our dedication to quality, innovation, and reliability.
With the highest standards of craftsmanship and engineering, we create beauty devices that set new benchmarks in performance and durability. PZLASER will deliver world-class solutions that enhance your practice and inspire confidence in every user.